You’ve all had one of “those days.” Maybe you had a tough time sleeping. Maybe you ran out of coffee. Or maybe you just felt a little bit off. Then you head into work and everything seems to take forever. You have a few missed connections with your clients or teammates. By the time you head home for the day you realize you didn’t really get anything done. The manufacturing process can be the same way. If it’s not firing on all cylinders, it’s hard to get the most out of each day. Marcus Lemonis would tell you the key to efficient manufacturing is “People, process, and product.” In this article, we’ll get into the specifics of what that actually looks like in a factory-setting so you can turbocharge your manufacturing process.
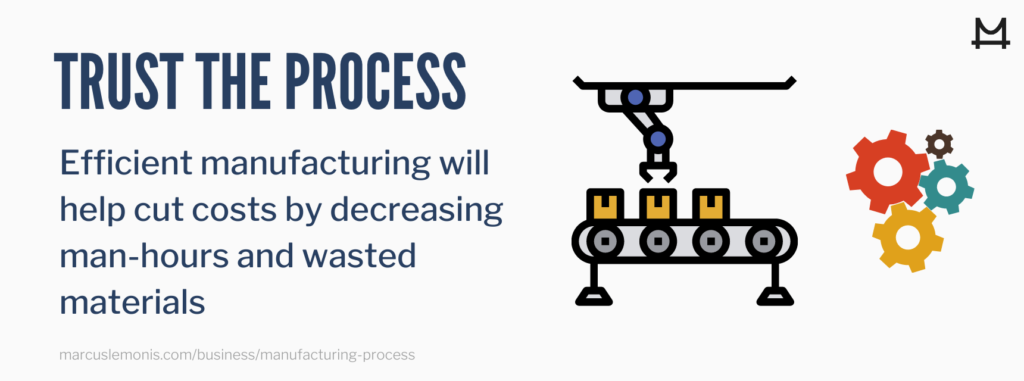
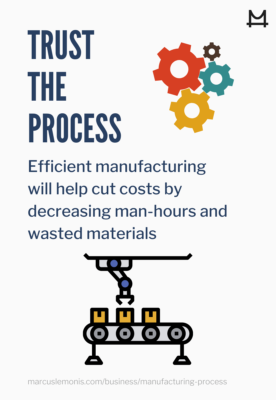
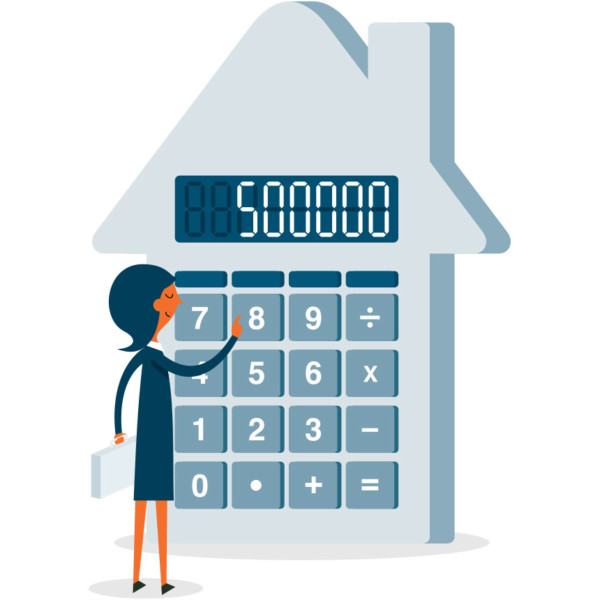
How to Develop a Good Manufacturing Process
- Evaluate Your Manufacturing Line
- When Marcus paid a visit to a Massachusetts-based drum manufacturer, he was impressed by the amount of care that went into making each hand-crafted drum. But the owners painted a pretty dicey picture of their situation, explaining that some of the orders took six or seven months to fill. That raised an eyebrow, so Marcus paid special attention to their manufacturing process. He noticed that materials were everywhere and workers felt overwhelmed by a climate of confusion. So, Marcus helped them install a simple and consistent flow that increased clarity, output, and improved turnaround.
It was enough to land the company contracts with huge chains like a national musical instrument retailer and an international music school. This lesson can be applied to any company’s process – no matter the size. Even if you advertise the time and care that goes into handcrafting each product, there’s still something to be said for organized and efficient manufacturing. Take a hard look at your line, be honest about what’s working and what isn’t, and you’ll be closing more deals in no time.
2. Assign a Dollar Value to Everything
-
- While you’re putting your manufacturing process under the microscope, it’s important to know how much you’re spending in each phase of the game. This helps you identify your biggest areas for improvement. Marcus brought this lesson to life when he worked with a high-end furniture company in California that catered mostly to commercial clients. The company was getting a ton of work, bringing in several million dollars in sales, but still losing money. Marcus learned it was because of their margins, which were under 30% and needed to be closer to 50%. This pointed to an efficiency problem, which Marcus figured out through his well-known “Know your numbers” approach. He knew that the furniture company could create more efficient manufacturing through a partnership with one of his other holdings, another furniture company which he had already helped implement a tried and true process. Can you learn something similar? How much does a bottleneck cost you? How much do you spend fixing quality issues? How much does shipping cost? How much are you spending on labor? How about materials? Make sure to know your numbers, because they’re trying to tell you a story.
3. Set Manufacturing-Specific Goals
-
- You’re out there making moves because you’re a goal-oriented person. But think about bringing that mindset to your manufacturing process as well. Have you set goals for quality, output, and margins? Do your goals follow the “S.M.A.R.T. Method” of being specific, measurable, achievable, relevant, and time-bound? If you’re not hitting those goals, don’t be afraid to take an unflinching look at why, then create an actionable plan to tighten things up. A lot of movers and shakers are very big-picture thinkers, but without ultra-specific goals, it’s hard to pinpoint the cleanest path to efficient manufacturing. Think about a squeaky wheel. When you hear the noise, you don’t put grease on everything. Instead, you dial in on which wheel needs a little attention and then give that one wheel a little love. Specific goals in your manufacturing process will pave the way to specific solutions.
4. Engage Employees
-
- Manufacturing is the backbone of the company, but the nature of the work can be repetitive and monotonous. So, it’s important to have a process for keeping these critical team members engaged. Make sure you’re seeking out their feedback and are open to communication flowing up the ladder. This helps employees feel seen and heard, and keeps management abreast of any issues. Also, think about a system for rewarding a job well-done. This could be verbally acknowledging employees, profiling their achievements in a company newsletter, or maybe even creating a bonus structure. Further, consider assigning specific goals to each individual. It’s a form of accountability and allows you to assign credit when things go right. Not only can this lead to more efficient manufacturing, but Gallup found engaged teams are actually 21% more profitable.
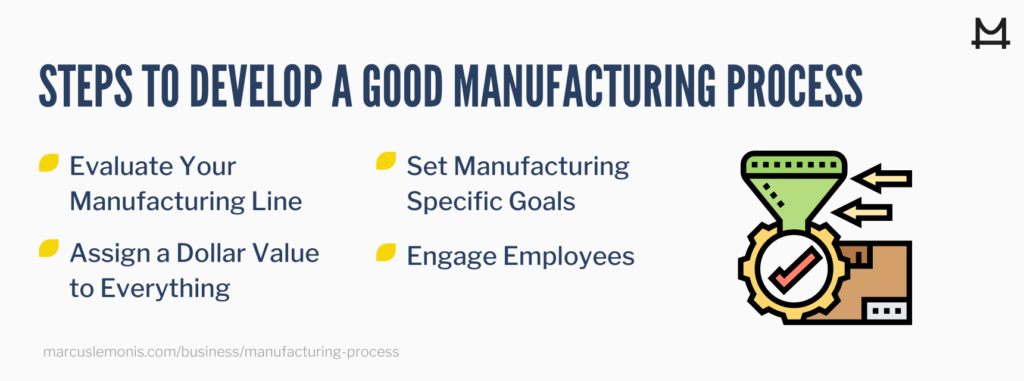
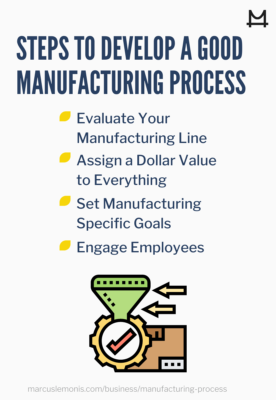
Ways to Improve Your Existing Process
- Reduce Waste
- Sometimes efficient manufacturing is less about doing something new, and more about making the most of what you already have. Think about ways to cut down on waste in terms of employee downtime, underutilized equipment, and over-ordering stock. That’s exactly what ThyssenKrupp did. They’re the largest materials company in Germany and execs felt their operation was underutilized. So, they kicked off a software development project to help with optimization, and ended up with a program that recommended stock levels, put their equipment on a maintenance schedule, and highlighted operations that were profitable enough to be expanded. This created a process so efficient they were capable of processing 2 million orders per year. You might think about using software in a similar way, but if software isn’t in the budget, a careful eye can uncover multiple low-tech solutions cut from the same cloth.
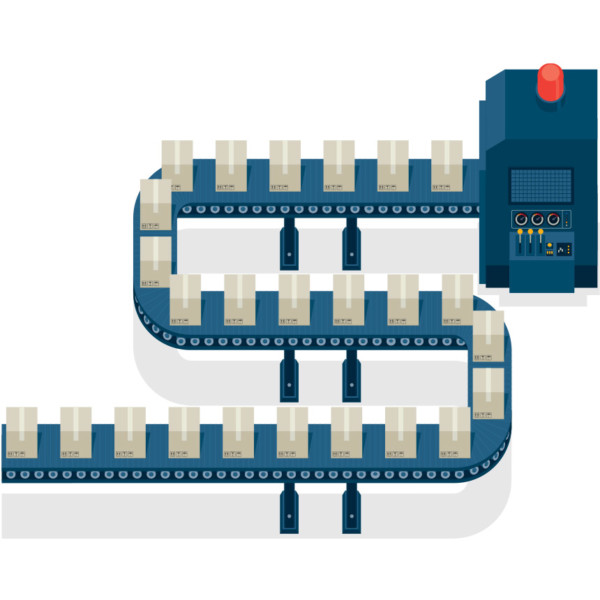
- Improve Training
- Think about training your employees with efficient manufacturing in mind. You know how we were saying that some of these tasks can end up being a little monotonous? If you train employees in a few different disciplines, this allows them to switch gears. They’ll not only be able to break up their day, but also cover for each other so you can keep your manufacturing process rolling when someone’s out of commission. You’ll also find that training gives you access to a whole new world of equipment. Can you benefit from a forklift? How about a pallet jack? An indoor lift, maybe? The Occupational Safety and Health Commission requires training before you operate any equipment of this type. So, a little extra training for your team might open up a whole new world for your manufacturing process.
- Standardize Your Manufacturing Process
- Standardization is one of the biggest things Marcus tried to drive home when he visited a third-generation family-owned furniture company in South Florida. He noticed the company, especially the grandson, had really high quality standards for themselves. But they weren’t always meeting their own lofty expectations. Marcus had a hunch it was because they didn’t have a quality control manager. He also noticed that some employees would promise delivery dates that forced production to rush their craft. So, Marcus helped standardize their manufacturing process. Everything went through the same steps, which meant everything ended up with the same quality. He also nominated the grandson to be head of quality control, requiring him to go through a uniform checklist as he inspected each order on its way out. This increased quality, reduced the amount of times customers sent back orders, and improved margins by reducing man-hours.
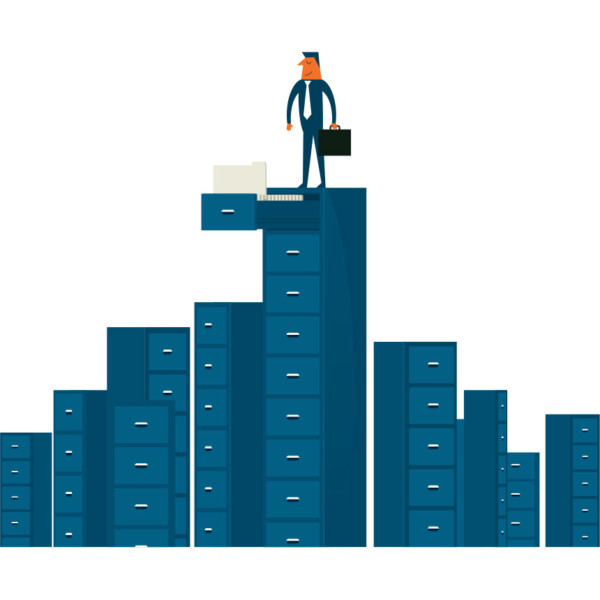
- Organize Everything
- Simply put, you need to know where to find everything, especially as your operation begins to grow. Can you find order #10792 in a warehouse the size of a football field? That’s exactly what Black & Decker tried to address at their massive factory in Mexico. They worked with Cisco to incorporate The Internet of Things (IoT) technology. This was a monumental upgrade that basically just allowed everyone to know where everything was at all times. This meant a simplified operation with less labeling errors. It also notified them automatically if something wasn’t where it should be. Further, it allowed managers to track progress and speed up or slow down the line accordingly. This increased their output by 10%, but you don’t need the IoT to run a tight ship. Are you organized enough to find a needle in a haystack?
- Manage Equipment Failures
- When it comes to equipment, a lot of people don’t think about maintenance until after something breaks down. But the name of the game is really preventative maintenance. Think about it. Would you rather go to the dentist for a minor tune-up once every six months? Or would you rather wait until your entire mouth is filled with cavities? Now, think about your car. Would you rather get routine $30 oil changes? Or would you rather just wait until your engine completely fails while you’re driving through the desert? The equipment in your factory is the same way. Educate yourself on the maintenance schedule and then assign the follow-up to one specific person – or a team of people depending on your company size. Also, as tempting as it might be to save a couple of bucks and come up with a corner-cutting workaround, think about the long-run. A battered piece of equipment operating at half capacity increases man hours and reduces output. It might be time to spring for a new machine. Don’t think of it as taking a loss. Think of it as making an investment.
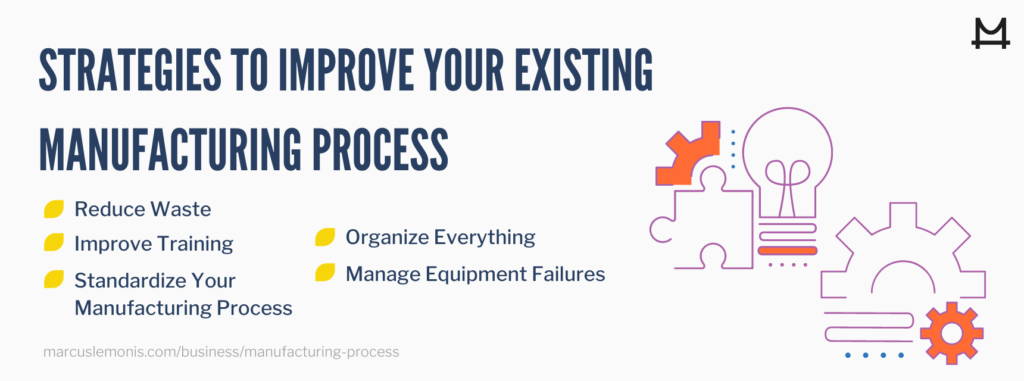
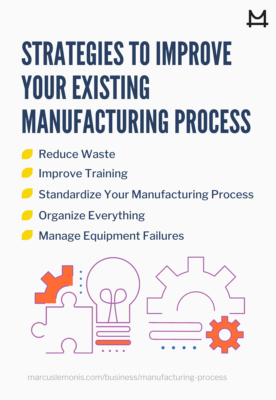
Benefits of Efficient Manufacturing
It goes without saying that efficient manufacturing is “Position A,” but you’re probably asking yourself whether it’s worth investing the time and money it would take to actually get there. So, if you’re still thinking it over, Marcus would tell you: “Trust the process.” You’ll help cut costs by decreasing man-hours and wasted materials. The environment will thank you because you’re decreasing the amount of time you run your factory on a per unit basis. You’ll increase sales through higher quality. You’ll increase output by optimizing your manufacturing process. You can even improve your company’s image by putting a consistently high-quality product out into the world. The hope is that when you see all those benefits laid out end-to-end, you’re not thinking about “if” you’ll optimize your manufacturing process, but “when.”
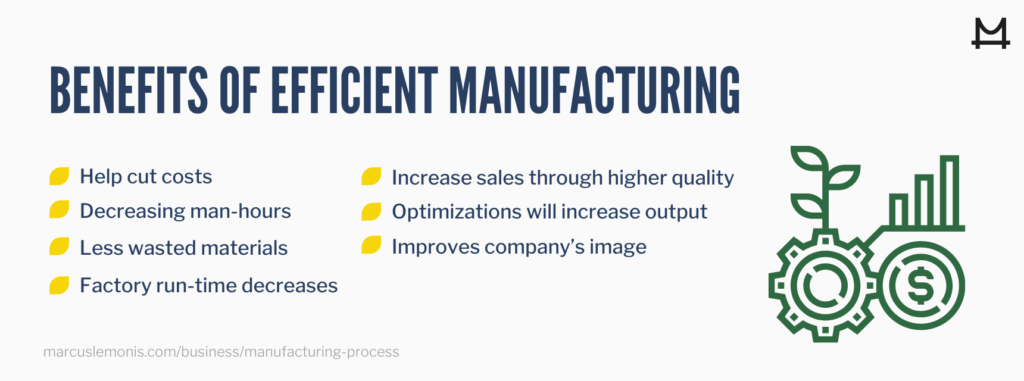
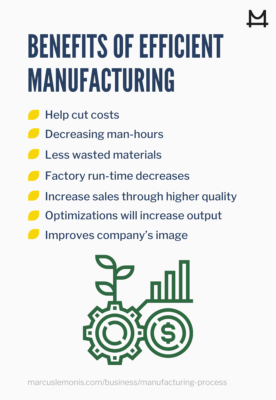
Have you ever known someone who bought a treadmill for their basement? Spoiler alert: the odds are their treadmill is drastically underutilized. Most people put all the money and effort into setting one up, but never get the most out of it. You don’t have to let that happen to your manufacturing process, because now you understand the importance of setting it up for efficiency, how to improve it along the way, and all the reasons it’s worth your while. Now all you have to do is commit to running the manufacturing marathon and your company will be in great shape.
- Do you have a good/efficient manufacturing process currently for your business?
- Are there any areas you can improve?
MindTools.com. (n.d.). SMART goals: how to make your goals achievable. Retrieved from
https://www.mindtools.com/pages/article/smart-goals.htmHarter, J. (2017, April 12). The right culture: not just about employee satisfaction. Retrieved from
https://www.gallup.com/workplace/236366/right-culture-not-employee-satisfaction.aspxMicrosoft.com. (2019, June 13). Materials services ‘keeps calm and carries on’ – with its new alfred AI solution to optimize its logistics network. Retrieved from
https://news.microsoft.com/europe/features/thyssenkrupp-materials-services-keeps-calm-and-carries-on-with-its-new-alfred-ai-solution-to-optimize-its-logistics-network/CertifyMe.net. (n.d.). Do you need a license to drive a forklift? Retrieved from https://www.certifyme.net/need-license-drive-forklift/
Cisco.com (n.d.). Internet of things case study: Stanley Black & Decker. Retrieved from
https://www.cisco.com/c/en/us/solutions/industries/manufacturing/connected-factory/automation/stanley-black-decker.html